China Plastic Injection Molding: Revolutionizing the Manufacturing Industry
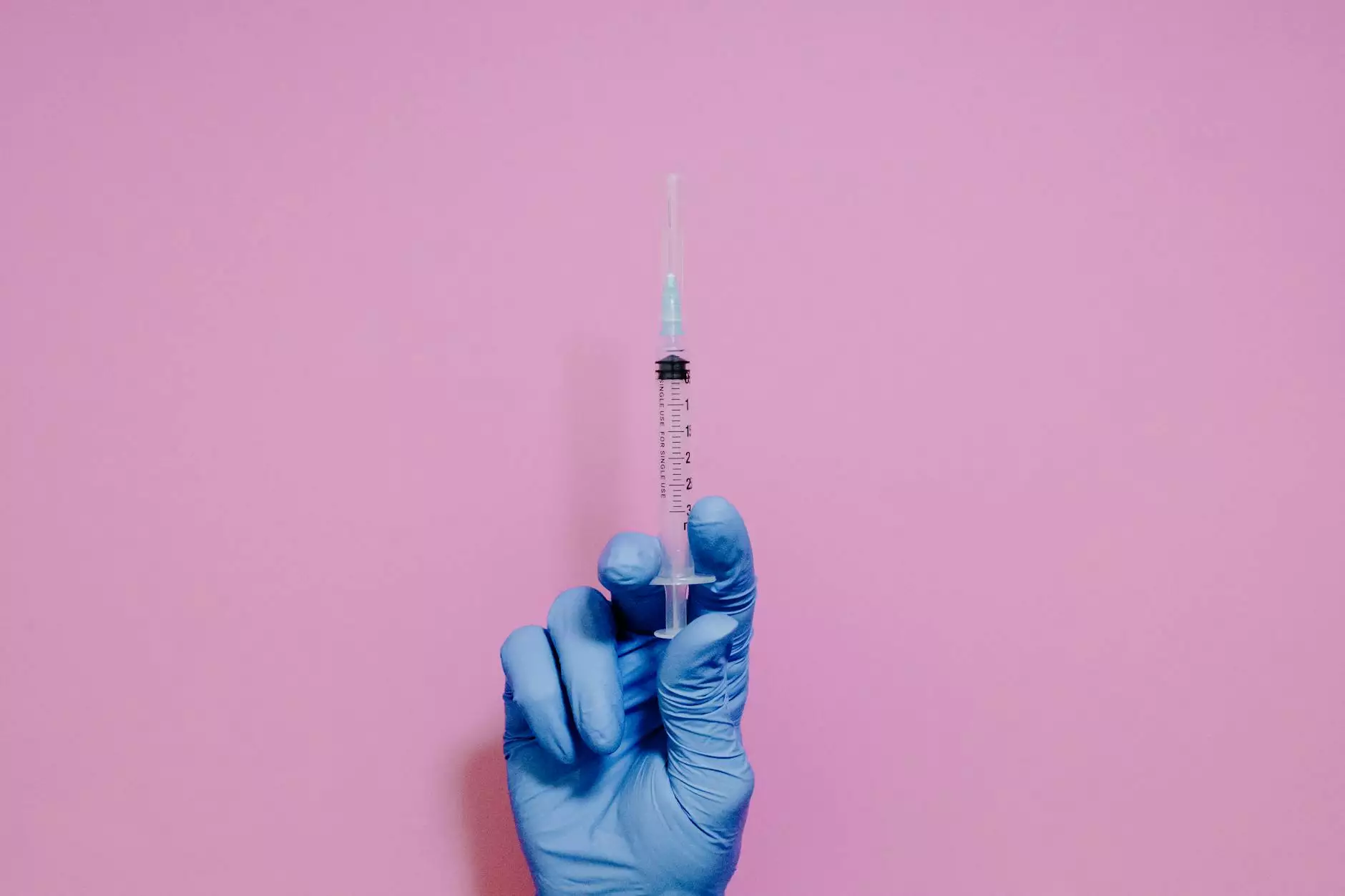
China plastic injection molding has become a cornerstone of the modern manufacturing landscape. As global demand for high-quality and cost-effective plastic products continues to rise, Chinese manufacturers have honed their skills and technologies to meet these requirements with precision and efficiency. This article delves into the intricacies of plastic injection molding in China, exploring its processes, advantages, and the leading manufacturers like Hanking Mould.
Understanding Plastic Injection Molding
Plastic injection molding is a manufacturing process where plastic materials are melted and injected into a mold to create specific shapes and structures. This versatile process is employed across multiple industries, including automotive, consumer goods, electronics, and medical devices. The primary steps involved in the plastic injection molding process include:
- Material Selection: Choosing the right plastic resin (such as ABS, PVC, or polycarbonate) is crucial for achieving the desired characteristics in the final product.
- Heating and Melting: The selected resin is heated until it melts, making it pliable for molding.
- Injection: The molten plastic is injected into a mold cavity under high pressure.
- Cooling: The material cools and solidifies, taking the shape of the mold.
- Mold Opening: Once cooled, the mold opens to release the finished product.
- Finishing: Additional processes such as trimming, painting, or assembly may enhance the product's final quality.
The Advantages of China Plastic Injection Molding
Choosing China plastic injection molding offers numerous benefits that make it a preferred choice for businesses worldwide. Some of these advantages include:
- Cost-Effectiveness: China is renowned for its competitive pricing, primarily due to lower labor costs and advanced manufacturing capabilities.
- High Efficiency: Injection molding is a quick process that allows for the mass production of high-quality parts in a short timeframe.
- Design Flexibility: The technology enables intricate designs and fine details that can be tailored to specific requirements.
- Material Variety: A wide range of plastic materials can be used, allowing manufacturers to choose the best options for their needs.
- Scalability: The production process can be easily scaled up or down to meet fluctuating demand without significant changes in manufacturing operations.
The Role of Hanking Mould in the Industry
Hanking Mould stands out as a leading plastic injection mould manufacturer in China. With an unwavering commitment to quality and innovation, Hanking Mould has established itself as a trustworthy partner for many businesses looking to leverage China plastic injection molding capabilities. Some key factors that define Hanking Mould's success include:
Quality Assurance
The team at Hanking Mould is dedicated to maintaining high-quality standards throughout the injection molding process. They employ stringent quality control measures at every stage to ensure that the final products meet or exceed international standards.
Advanced Technology
Utilizing state-of-the-art technology, Hanking Mould ensures that their processes remain at the forefront of innovation. This includes adopting the latest machinery, software, and methodologies in plastic injection molding.
Expert Team
The expertise of Hanking Mould’s engineers and technicians is a pillar of their operations. With years of experience and continuous training, the team is well-versed in tackling challenges associated with complex molding requirements.
Customized Solutions
Hanking Mould understands that each business has unique needs. They offer highly customizable solutions tailored to individual clients' specifications, ensuring that every product is engineered to perfection.
Industry Applications of Plastic Injection Molding
The versatility of plastic injection molding allows it to be utilized in countless applications across various industries, including:
1. Automotive Industry
Injection molded parts such as dashboards, door panels, and even engine components are crucial in modern vehicles. The lightweight yet durable plastic materials used can improve fuel efficiency without compromising safety.
2. Consumer Products
Household items ranging from storage containers to kitchen utensils are made using injection molding, providing durability and cost-effectiveness in large production runs.
3. Electronics Sector
From casings for smartphones to components for home appliances, plastic injection molding serves as the backbone for electronics manufacturing, allowing for intricate designs and high-density packing.
4. Medical Devices
The healthcare industry benefits immensely from injection molded plastic components that can be manufactured in sterile environments, meeting stringent regulatory requirements with ease.
Sustainability in Plastic Injection Molding
As environmental concerns rise, the industry faces pressure to adopt more sustainable practices. In this regard, Chinese manufacturers are making strides in the following areas:
- Recyclable Materials: The use of recyclable plastics reduces environmental impact and fosters a circular economy.
- Energy Efficiency: Advanced machinery and processes consume less energy, translating to lower carbon footprints.
- Waste Reduction: Innovations in process design minimize material waste during production.
Choosing the Right Plastic Injection Mould Manufacturer
When selecting a plastic injection mould manufacturer, several factors should be considered to ensure successful collaboration and high-quality production:
1. Experience and Reputation
Seek out manufacturers with a strong track record and positive client feedback. Experience often correlates with reliability in quality and service.
2. Technological Capabilities
Examine the equipment and technology used in the manufacturing process. Modern machinery can significantly improve product quality and production efficiency.
3. Customer Service
Effective communication and strong customer support are essential for addressing any issues that arise during the project timeline.
4. Portfolio of Work
Review previous projects to get an understanding of the manufacturer’s capabilities. A diverse portfolio suggests flexibility and expertise.
The Future of Plastic Injection Molding in China
The future of plastic injection molding in China looks promising, as advancements in technology and manufacturing processes continue to evolve. Trends to watch include:
- Industry 4.0 Integration: The incorporation of smart manufacturing and IoT will drive efficiency and real-time monitoring of production processes.
- Bio-Based Plastics: Innovations in sustainable materials will promote greater adoption of eco-friendly alternatives in manufacturing.
- Increased Automation: Automation technologies will reduce human error and improve production rates while maintaining quality.
Conclusion
In conclusion, China plastic injection molding is an essential component of the global manufacturing sector, offering unparalleled advantages in efficiency, cost, and customization. With companies like Hanking Mould leading the charge, the industry is set for continued growth and innovation. As businesses increasingly turn towards injection molding for their plastic needs, understanding the nuances of this process will empower them to make informed decisions that drive success and sustainability.
For more information about our products and services at Hanking Mould, please visit our website: hanking-mould.com.