Understanding Plastic Injection Moldings
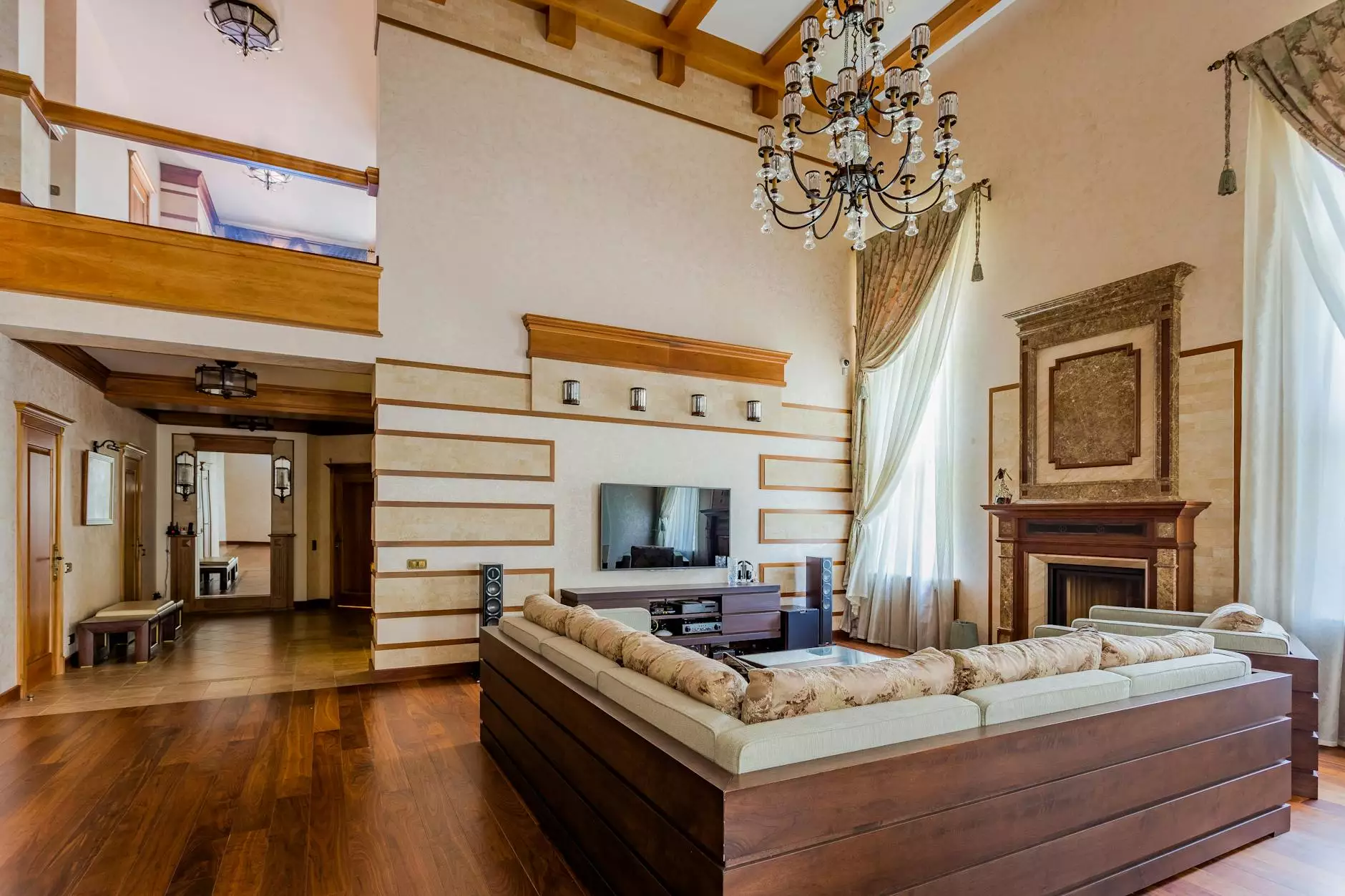
The world of manufacturing is continuously evolving, thanks to advanced techniques and processes that enhance productivity and efficiency. Among these techniques, plastic injection moldings stand out as a crucial method that shapes a plethora of industries. This article aims to help you understand the intricacies of plastic injection moldings, their applications, advantages, and the future of this essential technique.
The Basics of Plastic Injection Moldings
At its core, plastic injection molding is a manufacturing process used to create parts by injecting molten material into a mold. This technique is particularly favored for its ability to produce high volumes of identical, complex shapes with precision. The process can be broken down into several critical steps:
- Material Selection: The first step involves selecting the appropriate plastic material, which can range from thermoplastics to thermosetting plastics. Each material offers unique properties, making it suitable for various applications.
- Melting the Material: Once the material is chosen, it is heated until it becomes molten. This molten plastic is then ready to be injected into the mold.
- Mold Injection: The molten plastic is injected into a pre-designed mold under high pressure. This step requires precision to ensure the mold is filled completely and evenly.
- Cooling: After the mold is filled, the plastic is allowed to cool and solidify. Cooling time can vary based on the type and thickness of the material.
- Mold Removal: Once cooled, the mold is opened, and the finished part is ejected. Quality checks are usually conducted at this stage.
Applications of Plastic Injection Moldings
Plastic injection moldings are utilized across a broad spectrum of industries, making them a versatile option for manufacturing needs. Here are several key applications:
- Automotive Industry: Plastic parts such as dashboards, bumpers, and interior components are commonly produced using injection molding due to their lightweight and durable nature.
- Consumer Products: Everyday items like containers, toys, and appliances often utilize injection-molded plastics, allowing for intricate designs and mass production.
- Medical Devices: The medical field benefits significantly from plastic injection molding, producing components that require strict compliance with hygiene and security standards.
- Aerospace Applications: The aerospace industry leverages this technology for lightweight yet strong components that improve fuel efficiency.
- Electronics: Many electronic housing parts are manufactured using injection molding, providing a secure and aesthetically pleasing casing for vital devices.
Advantages of Plastic Injection Moldings
Choosing plastic injection moldings comes with a host of benefits, making it a preferred manufacturing process for many companies. Here are some significant advantages:
1. Cost-Effectiveness
One of the most compelling reasons to adopt plastic injection molding is its cost-effectiveness. The ability to produce large quantities of parts quickly translates to reduced labor costs and lower material waste, significantly enhancing profitability.
2. High Precision
Plastic injection moldings allow for high precision in the manufacturing process. The molds can be designed to produce parts that meet tight tolerances, ensuring that each item is almost identical to the last, which is essential for quality assurance in mass production.
3. Versatility in Design
Design versatility is another significant advantage of this process. Manufacturers can create complex shapes that would be challenging or impossible to achieve through other production techniques. This flexibility enables innovation in product design.
4. Material Variety
Injection molding accommodates a wide range of materials, including various plastics. This variety allows businesses to select materials based on desired characteristics such as strength, flexibility, and temperature resistance, tailored to the specific application.
5. Quick Production Cycles
The efficiency of plastic injection moldings results in quick production cycles, with some molds capable of producing thousands of parts in a single day. This rapid turnaround is essential for businesses needing to respond swiftly to market demands.
6. Minimal Waste
Since the injection molding process involves using only the required amount of material, waste is minimized. Excess plastic can often be reused in future productions, enhancing sustainability.
Challenges and Considerations
While the advantages of plastic injection moldings are significant, it is essential to recognize some challenges that may arise:
- Initial Investment: The upfront costs of creating molds can be high, which may deter smaller businesses or startups.
- Complexity in Design Changes: Once a mold is created, making design changes can be costly and time-consuming, necessitating careful planning during the design phase.
- Material Limitations: Not all plastics are suitable for every application, making material selection critical.
The Future of Plastic Injection Moldings
As technology advances, the future of plastic injection moldings looks promising. Emerging trends include:
1. Automation and Robotics
Incorporating automation in the injection molding process can further reduce production costs and enhance efficiency. Robots can handle repetitive tasks, allowing human workers to focus on higher-value activities.
2. Sustainable Practices
The drive towards sustainability is influencing the adoption of eco-friendly materials and processes in injection molding. Biodegradable plastics and recycling initiatives are gaining traction, encouraging manufacturers to consider environmental impacts.
3. Advanced Technologies
The integration of technologies like 3D printing is revolutionizing the mold-making process, allowing for rapid prototyping and shorter lead times. This hybrid approach can significantly improve the efficiency and flexibility of production.
4. Customization
As consumer preferences shift towards personalized products, the injection molding industry must adapt. Innovations that enable the customization of molded products will likely see increased demand.
Conclusion
In conclusion, plastic injection moldings play an indispensable role in modern manufacturing across various sectors, ranging from automotive to aerospace to consumer goods. The capabilities of this process, combined with its numerous advantages such as cost-effectiveness and design versatility, make it a cornerstone of manufacturing success. As businesses continue to evolve and industries adapt, the future of plastic injection molding looks bright, promising further innovations and improvements. Whether you're looking to delve into this manufacturing method or seeking to optimize your existing processes, understanding the value of plastic injection moldings will undoubtedly enhance your business strategy.
For more insights into plastic injection moldings and how they can benefit your industry, feel free to reach out to us at deepmould.net. We are committed to providing you with comprehensive solutions tailored to your manufacturing needs.