Unlocking Potential: **Purchasing Plastic Injection Mold Service**
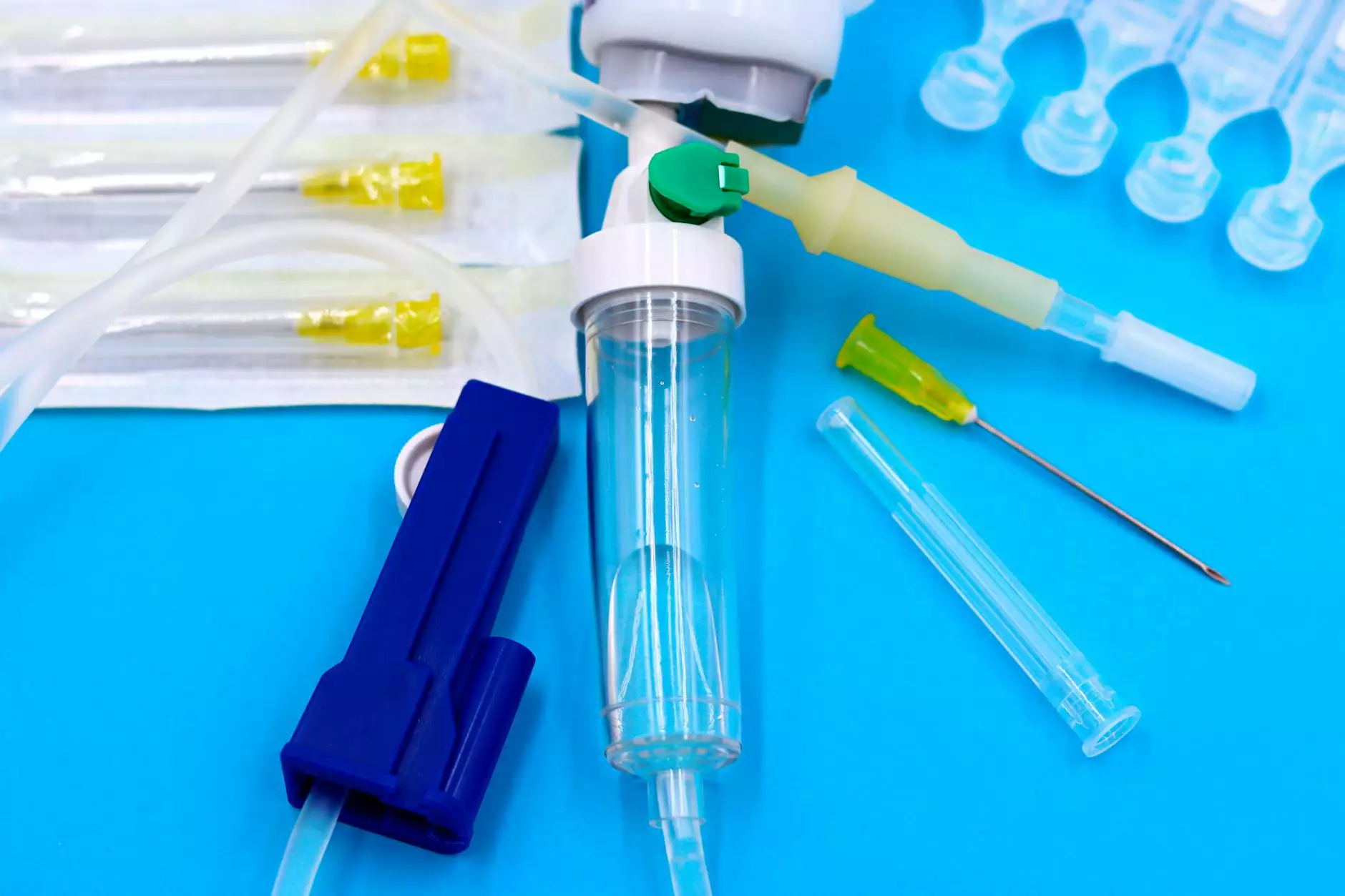
In the modern industrial landscape, the efficiency and versatility of manufacturing processes are pivotal for success. One of the standout methods in the realm of production is plastic injection molding. This sophisticated procedure allows for the creation of complex plastic parts at scale, making it an essential service for businesses in various sectors. If you're considering purchasing plastic injection mold service, this article will guide you through its multifaceted advantages, the process involved, and how to choose the right service provider to meet your needs.
Understanding Plastic Injection Molding
Plastic injection molding is a manufacturing process for producing parts by injecting molten material into a mold. The process begins with heating plastic granules until they reach a molten state, which are then injected into a pre-designed mold. Once cooled, the mold is opened, and the finished part is ejected. This method is renowned for its ability to produce high volumes of identical parts rapidly and efficiently.
Advantages of Purchasing Plastic Injection Mold Service
Investing in a plastic injection mold service presents several compelling advantages for businesses, including:
- Cost Efficiency: Mass production reduces the cost per part, making it a cost-effective choice for manufacturers.
- Precision Engineering: Injection molds can produce intricate designs with tight tolerances, ensuring high-quality outcomes.
- Material Versatility: A wide range of materials can be used, including thermoplastics and thermosetting plastics, allowing for customization based on specific needs.
- Rapid Prototyping: The speed of the process allows for fast changes and adjustments, which is vital in today’s fast-paced market.
- Environmental Considerations: Many injection molds are designed to minimize waste and reduce energy consumption, aligning with sustainable manufacturing practices.
Key Components of the Plastic Injection Molding Process
The plastic injection molding process involves several key components:
1. Mold Design
The mold is the centerpiece of the injection molding process. A well-designed mold is crucial to producing high-quality parts consistently. Factors to consider include:
- Draft Angles: Allow easy removal of parts from the mold.
- Cooling Channels: Ensure that the mold cools uniformly for consistent production.
- Gate Design: The entry point for the molten plastic, affecting the flow and cooling rates.
2. Material Selection
Choosing the right thermoplastic material is essential, as it affects the final product's strength, flexibility, and appearance. Popular materials include:
- ABS: Known for its impact resistance and toughness.
- Polyethylene: Offers excellent chemical resistance and is widely used in bottles and containers.
- Polypropylene: Known for lightness and resistance to fatigue, making it ideal for living hinges.
3. Injection Phase
In this phase, the heated plastic is injected into the mold at high pressure. This step is critical as it determines the part's structure and integrity.
4. Cooling Phase
After injection, the molten plastic must cool sufficiently before the mold can be opened. The cooling time depends on the thickness of the part and the material used.
5. Ejection Phase
Once cooled, the mold opens, and ejector pins remove the finished part. Proper design of the ejector system reduces the risk of part deformation.
Factors to Consider When Purchasing Plastic Injection Mold Service
When eyeing the purchase of plastic injection mold services, several factors should guide your choice:
1. Expertise of the Manufacturer
Choose a supplier with extensive experience in injection molding services. A seasoned manufacturer will understand the nuances of material selection, mold design, and production timelines.
2. Production Capabilities
Your provider should have the equipment and technology to handle your specific needs. This includes the ability to create molds with intricate designs, as well as the capacity to produce large volumes of parts efficiently.
3. Quality Assurance
Ensure that the manufacturer follows strict quality control protocols. Certifications like ISO 9001 can be indicators of a company's commitment to quality.
4. Customer Service
Strong communication and customer support are vital for a successful partnership. Your chosen provider should be responsive and willing to address your inquiries promptly.
5. Turnaround Time
In today's competitive market, time is often of the essence. Ask about the expected production timelines and how they handle delays.
Common Applications of Plastic Injection Molding
Plastic injection molding is employed across a wide range of industries due to its versatility. Some common applications include:
- Automotive Industry: Production of dashboard components, clips, and housings.
- Consumer Electronics: Cases and components for devices such as smartphones and tablets.
- Medical Devices: Manufacturing sterile and precise components for medical equipment.
- Toys: Creating fun, safe, and colorful toys for children that adhere to safety standards.
The Future of Plastic Injection Molding
The landscape of plastic injection molding continues to evolve. Advancements such as smart manufacturing, automation, and improved materials are shaping its future. Notably:
- Additive Manufacturing Integration: Combining 3D printing with traditional injection molding for rapid prototyping.
- Sustainability Trends: Increased emphasis on biodegradable and recycled materials to align with eco-friendly practices.
- Digital Twin Technology: Using simulations to optimize the injection molding process and predict outcomes before production begins.
Conclusion: The Smart Investment in Purchasing Plastic Injection Mold Service
Purchasing plastic injection mold service is more than just a business decision—it's a strategic investment in your company's future. By embracing this innovative manufacturing technique, you can achieve efficiency, precision, and scalability that is unparalleled.
Partnering with a reputable provider like Sumiparts.us ensures you leverage the best practices and expertise in the industry, allowing you to focus on what matters most—growing your business. If you're ready to explore how injection molding can transform your manufacturing capabilities, contact us today!